この記事では、5軸加工機を導入するメリット、中でも今回は工具の交換や消耗にかかる日々のコストについて【価格】をテーマに検証してわかりやすく記載しています。
日々稼働する5軸加工機の消耗品である先端工具は、意外とランニングコストがかかってしまいますよね。
現在立型3軸機を使用中で5軸加工機の導入を検討している方も、将来的に新らしくマシニングを購入しようと考えている方も参考になればという思いで書きますので、よろしくお願いします。
ここでそもそもなんで5軸加工機は選ばれているのか?
この疑問について「工具コスト」というテーマにしぼって解説していきます。
コンテンツ
【5軸加工機のメリット】加工物を傾けられることによるメリット
⑴5軸加工機なら形状精度が良くなる(なめらかになる)
まず第一のメリットは、加工物を傾けて加工できる点です。
加工物を傾けることによって、ボールエンドミルなどの先端で加工して面がむしれてしまう(※)のを避けられます。
傾けることでエンドミルの刃に沿った加工ができるので、仕上がりがキレイになり、時間も短縮できます。
なので、5軸加工機ならワークを傾けられるおかげで、ビビリが少なく加工面がなめらかに仕上がるのです。
当然、工具にも破損や摩耗の軽減などのメリットが出ます。
※ボールエンドミルは水平のワークに対し先端で直角に刃が入ってしまうと表面がザラついてさらにもう1段階手間をかけて仕上げが必要になります。
↓↓↓加工物を傾けて加工しているのがわかる動画(牧野フライス製作所)
⑵5軸加工機なら工具の突き出し長さが短くできる
5軸加工機ではワークを傾けることによって、使用する先端工具が短くて済むというメリットがあります。
3軸の加工機を稼働させている現場ではワークの形状によって仕方なく長い工具を使用していませんか?
長い工具を使う理由は以下です↓
■深い溝などの奥を削りたいとき
■工具がワークに干渉するのを避けたいとき
それではワークを傾けることができれば、どうでしょうか?
■溝の奥も斜めからの加工ができる
■ワークに干渉する心配がなくなる(少なくなる)
このように、干渉がなくなるので、その分長い工具を半分にしたりと、工具が短くて済みます。
⑶5軸加工機なら工具寿命が延びる、ランニングコストが減る
上記のように、5軸加工機なら工具長さを約半分にしての加工が可能であることがわかりましたね。工具突き出し長さが半分になれば計算上このようなメリットがあります。
■刃物の靭性が4倍に
■刃物の曲がりは1/8に
■切り屑排出量は9倍に
このように、明らかに工具の切削性はアップすると考えられています。
例えば長いエンドミルだと…
だいたいこのクラスで6000円前後です(独自に調べるとサイトでは¥5,770-でした)
このロングシャンクのエンドミルを2カ月に一回消耗品として仕入れるとします。
工場の規模にもよりますが、同じようなサイズ感の加工をしているマシニングが7台あった時の年間のランニングコストは
¥6000-×6回仕入×7台分=¥252,000-
年間25万円のコストとなります。
刃物の靭性が4倍なのでハイパー単純に計算すると
¥252,000÷4=63,000
252,000-63,000=189,000
年間18万9000円もお得になるということになります。
これはもうほんとにザックリとどんぶり勘定しただけですが、日々の工具コスト面では下がることは明らかですね。
買い替えじゃなく研磨に出している。という方もお得にはなります。(研磨だと費用は1本約3000円前後)
まとめ:工具へのランニングコストがお得に
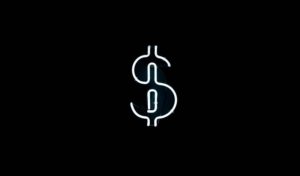
このように、ランニングコストが下がって毎年の固定費用がリーズナブルになる。という検証結果ですが、みなさんいかがでしょうか?
5軸加工機のメリットであるワークが傾くという点、実はコスト面だけではありません。
芯出し時間も短縮できるメリットがあります。
5軸加工機の芯出し時間に関して詳しくはこちらで解説してます↓

5軸加工機での省人化に関してはこちら↓
